高精度に噛み合う歯形で金型駒を直彫り加工
海外のお客様からの紹介で、特殊なフェースギヤ用の金型駒を製作しました。
スケジュールの都合上、試作部品で歯形の評価を頂く時間は無く、歯形解析をした上で、金型用の駒を直彫りで一発加工して納めました。
実は、この案件は数か月前に既に引き合いが有り、見積りを御提示しておりましたが、海外の地場業者の見積り価格との差が大きかったため、ユーザー様ではコスト優先で、地場業者に金型発注しておりました。しかしながら、歯形精度の不備に起因する異音が発生して、製品機能上の大きな問題となり、これが自力で改善できなかったため、改めて御依頼がありました。
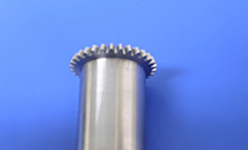
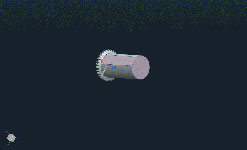
弊社固有技術による問題解決の提案
①量産用の金型を製作したものの歯形精度が悪く、干渉による異音が発生。 ②量産スケジュールが迫っており、改めて試作部品を製作して評価をやり直す時間は無く、高精度な噛み合いを実現する金型を、限られた期日までに一発での製作が必要。
弊社では特殊な歯形の歯車試作に豊富な経験があり、特にフェースギヤの歯形設計については、3DCAD上での歯形解析によって、干渉を排除し高効率の噛み合いを実現するノウハウがありました。そこで、相手ピニオンと高精度に噛み合う歯形を3D設計した上で、5軸複合機で金型駒を直彫りすることにより、精度と工期短縮を両立した工法を御提案しました。
外端側と内端側で曲率の異なる歯面に、軸直交で同一ピッチの平歯車やハスバ歯車を噛み合わせるフェースギヤは、外端側と内端側では歯面の形状が異なり、かなり変則的な歯形となります。更に今回の案件は軸直交ではなく、軸角が広角で、部品のイメージとしては内歯車に近い形状となるため、解析による3D歯形生成が必須でした。 相手ピニオンの歯形とバックラッシ量を勘案して歯形を生成し、更に成形収縮率を考慮して拡大処理し、これを反転させて金型駒加工用のモデルとしました。
弊社には3軸機、5軸機と複数の設備がありますが、今回は金型用のプリハードン材など、硬度のある素材を加工可能な5軸複合加工機を使用して加工しました。 通常、歯車用の金型駒の加工は、ホビングや放電加工などが一般的ですが、事前にホブカッターや放電マスターを製作する期間が必要となり、工期短縮の弊害となります。また、カッターやマスターも誤差ゼロではない上に、これにホブ加工や放電加工の加工誤差が加わるため、精度コントロールが難しい側面もあるように思えます。これに対し、金型駒に直彫りの場合は、工期短縮と精度コントロールの両立が容易というメリットが有ります。 弊社では通常、歯車歯面の面精度は、スカラップハイト1/1000に設定していますが、金型用ということで7/10000を目指して加工しました。幸い保持と芯出しが容易な形状だったので、加工自体には問題はありませんでした。
この駒を組み込んだ金型で成形した結果、懸案の異音問題は一発解決したとのことです。
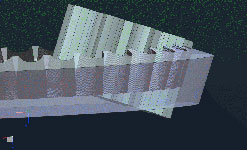
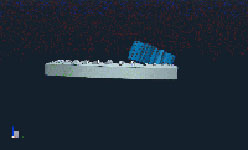